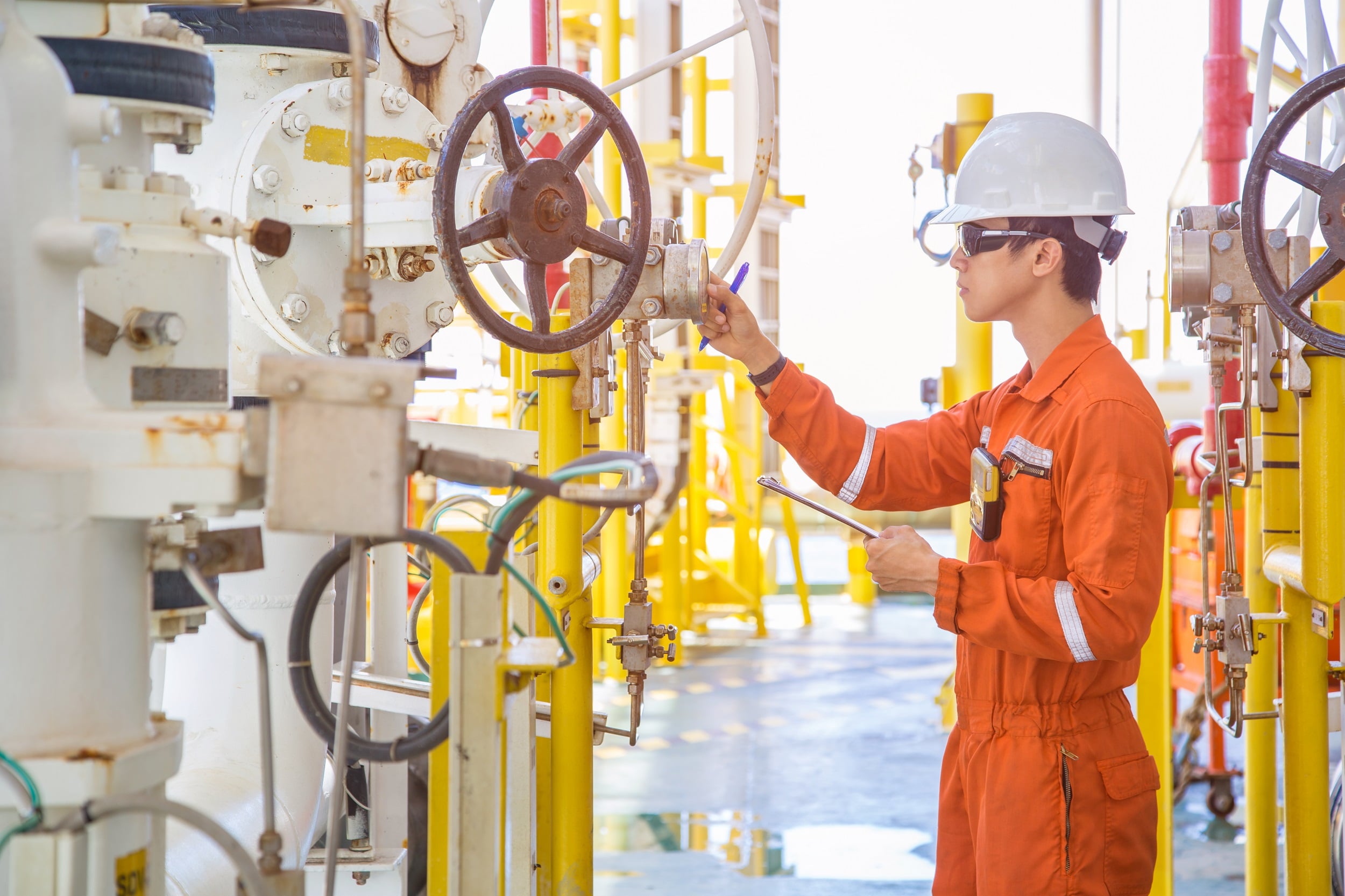
Vendor Inspection is the inspection and validation of new equipment. Vendor inspection of equipment can take place throughout the supply chain - during the manufacturing process, prior to the equipment leaving manufacturing site as well as during transportation and on-site arrival.

How would Vendor Inspection benefit clients?
Having the capability to carry out inspection work at the supplier’s site gives the client a level of confidence which allows them to control and manage risk across their entire supply chain.
With an experienced team of third-party inspectors to choose from, the client will be guaranteed a quality service that will be delivered whilst adhering to local and international standards, always ensuring compliance and safety.



Various types of inspection services that Brunel provides.
Third Party Inspection
- Ensure that products ordered by client meet compliance standards
- Inspect and ensure quality and technicality of product
- Perform Welding NDT, Leak Test, FAT, etc., inspections
- Qualify and inspect Electrical Instruments as well as Coating Inspection checks
- Evaluate and certify goods (equipment) before shipping
Vendor Quality Audit
- To ensure vendor’s integrity and their management responsibility
- Checking of Quality Management system and processes
- To minimise cost and improve quality
Vendor Expedition
- Surveillance visits made to track the progress of ordered equipment
- To reduce delays and speed up the fabrication process by identifying the issues
- To ensure that the delivery schedule will be met
Remote Inspection
- Providing seamless inspection service
- Covering inspection via attendance “Inspection Link”
- Maintain business continuity & remote security with Global Cloud Proxy
- Ensure inspectors remain secure while working from home under pandemic conditions

Your Partner for Project-based Services
Are you in need of technical inspection services? Talk to us about your needs today!
Brunel's Global Vendor Inspection Team